National Emission Standard for Hazardous Air Pollutants (NESHAP) for Metal Fabrication and Finishing Source Categories
40 CFR Part 63 Subpart XXXXXX (6X)
NESHAP 6X Q&A Revised by EPA in 2020. Overview
Applicability
Requirements
Enforcement Authority
More resources
Overview
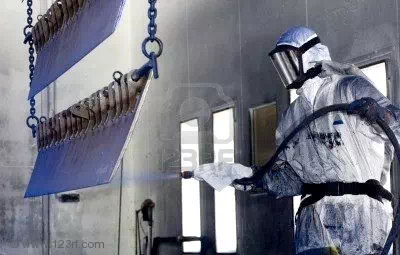
In 2008, EPA promulgated National Emission Standard for Hazardous Air Pollutants (NESHAP) for Metal Fabrication and Finishing Source Categories (6X) requirements to reduce air pollution of compounds of metals such as cadmium, chromium, lead, manganese and nickel from nine metal fabrication and finishing source categories. These compounds pose health risks to anyone who breathes the air when these fumes are present. These compounds are emitted to the air from various operations at metal fabrication and finishing plants, including spray painting.
Existing sources must be in compliance with the regulation before July 25 2011. New sources must be in compliance when they begin to operate.
The rule applies ONLY to area sources where the primary activity of the facility is in one of the following nine source categories:
- Electrical and Electronic Equipment Finishing Operations (including motor and generator manufacture, and electrical machinery, equipment, and supplies, not elsewhere classified);
- Fabricated Metal Products;
- Fabricated Plate Work (Boiler Shops);
- Fabricated Structural Metal Manufacturing;
- Heating Equipment, except Electric;
- Industrial Machinery and Equipment Finishing Operations (including construction machinery manufacturing; oil and gas field machinery manufacturing; and pumps and pumping equipment manufacturing);
- Iron and Steel Forging;
- Primary Metal Products Manufacturing; and
- Valves and Pipe Fittings.
If you don’t use these codes, then you are not subject to 6X, but still may be subject to 40 CFR Part 63 Subpart HHHHHH, NESHAP Paint Stripping and Miscellaneous Surface Coating Operations at Area Sources (6H). However, you should be aware that the facility is only subject to one rule, either 6H or 6X, so if the facility is subject to 6X, it is not subject to 6H.
A more detailed description of the affected source categories is included in the text of the rule, available at https://www.epa.gov/stationary-sources-air-pollution/metal-fabrication-and-finishing-source-categories-national-emission
The following summarizes the requirements for spray painting. For other operations, such as abrasive blasting, welding and polishing, see the full text of the regulation.If you own or operate a new or existing spray painting affected source, you must implement the following nine management practices. Keep in mind that these requirements do not apply when spray-applied paints that do not contain metal finishing hazardous air pollutants (MFHAP) (defined to be the compounds of cadmium, chromium, lead, manganese, and nickel, or any of these metals in the elemental form with the exception of lead).
1. Standards for spray painting for MFHAP control. The following rules are related to spray booths. These requirements do not apply to affected sources located at Fabricated Structural Metal Manufacturing facilities or affected sources that spray paint objects greater than 15 feet (4.57 meters), that are not spray painted in spray booths or spray rooms.
-
Spray booths or spray rooms must have a full roof, at least two complete walls, and one or two complete side curtains or other barrier material so that all four sides are covered. The spray booths or spray rooms must be ventilated so that air is drawn into the booth and leaves only though the filter. The roof may contain narrow slots for connecting fabricated products to overhead cranes, and/or for cords or cables.
All spray booths or spray rooms must be fitted with a filter technology that is demonstrated to achieve at least 98 percent capture of MFHAP.
You must perform regular inspection and replacement of the filters in all spray booths or spray rooms according to manufacturer's instructions, and maintain documentation of these activities.
As an alternative compliance requirement, spray booths or spray rooms equipped with a water curtain that are operated and maintained according to the manufacturer's specifications and that achieve at least 98 percent control of MFHAP, may be used in lieu of the spray booth or spray room requirements.
2. Standards for spray painting application equipment of all objects painted for MFHAP control. All paints applied via spray-applied painting must be applied with a high-volume, low-pressure (HVLP) spray gun, electrostatic application, airless spray gun, air-assisted airless spray gun, or an equivalent technology that is demonstrated to achieve transfer efficiency comparable to one of these spray gun technologies for a comparable operation, and for which written approval has been obtained from EPA.
3. Spray system recordkeeping. You must maintain documentation of the HVLP or other high transfer efficiency spray paint delivery methods.
4. Spray gun cleaning. All cleaning of paint spray guns must be done with either non-HAP gun cleaning solvents, or in such a manner that an atomized mist of spray of gun cleaning solvent and paint residue is not created outside of a container that collects the used gun cleaning solvent. Spray gun cleaning may be done with, for example, by hand cleaning of parts of the disassembled gun in a container of solvent, by flushing solvent through the gun without atomizing the solvent and paint residue, or by using a fully enclosed spray gun washer. A combination of these non-atomizing methods may also be used.
5. Spray painting worker certification. All workers performing painting must be certified that they have completed training in the proper spray application of paints and the proper setup and maintenance of spray equipment. The minimum requirements for training and certification are described in the regulation. The spray application of paint is prohibited by persons who are not certified as having completed the training. The requirements of this paragraph do not apply to the students of an accredited painting training program who are under the direct supervision of an instructor who meets the training requirements. Also, the training requirements do not apply to operators of robotic or automated painting operations.
6. Spray painting training program content. Each owner or operator of an affected spray painting affected source must ensure, certify and maintain records that all new and existing personnel, including contract personnel, who spray apply paints are trained in the proper application of paints. The training program must include:
Spray gun equipment selection, set up, and operation, including measuring paint viscosity, selecting the proper fluid tip or nozzle, and achieving the proper spray pattern, air pressure and volume, and fluid delivery rate.
Spray technique for different types of paints to improve transfer efficiency and minimize paint usage and overspray, including maintaining the correct spray gun distance and angle to the part, using proper banding and overlap, and reducing lead and lag spraying at the beginning and end of each stroke.
Routine spray booth and filter maintenance, including filter selection and installation.
Environmental compliance with the requirements of this 6X regulation.
Each owner or operator of an affected spray painting source must also have a description of the methods to be used at the completion of initial or refresher training to demonstrate, document, and provide certification of successful completion of the required training. Alternatively, owners and operators who can show by documentation or certification that a painter's work experience and/or training has resulted in training equivalent to the required training are not required to provide the initial training for these particular painters.
7. Records of spray painting training. You must maintain records of employee training certification for use of HVLP or other high transfer efficiency spray paint delivery methods.
8. Spray painting training dates. All new and existing personnel at an affected spray painting affected source, including contract personnel, who spray apply paints must be trained by the applicable compliance date:
If your source is a new source, all personnel must be trained and certified no later than January 20, 2009, 180 days after startup, or 180 days after hiring, whichever is later. Training that was completed within 5 years prior to the date training is required, and that meets the requirements of this regulation satisfies this requirement and is valid for a period not to exceed 5 years after the date the training is completed.
If your source is an existing source, all personnel must be trained and certified no later than July 25, 2011, or 180 days after hiring, whichever is later. Worker training that was completed within 5 years prior to the date training is required, and that meets the requirements specified of this regulation, satisfies this requirement and is valid for a period not to exceed 5 years after the date the training is completed.
9. Duration of training validity. Training and certification will be valid for a period not to exceed 5 years after the date the training is completed. All personnel must receive refresher training that meets the requirements of this regulation and be re-certified every 5 years.
There also are reports that facilities must submit.
Initial Notification – must be submitted by July 25, 2011 for existing sources and 120 days after startup for new sources. This must be submitted by every facility in one of the nine source categories whether or not any process at the facility is subject to the standards and management practices.
Notification of Compliance Status Report – must be submitted by November 22, 2011 for existing sources and 120 days after initial startup for new sources.
Annual certification and compliance reports.
NESHAP 6X can be implemented and enforced by EPA or a delegated authority such as your state, local, or tribal agency. If the EPA has delegated authority to your state, local, or tribal agency, then that agency, in addition to EPA, has the authority to implement and enforce this regulation. You should contact your EPA Regional Office to find out if implementation and enforcement of this subpart is delegated to your state, local, or tribal agency.